14.0 Final Design and Construction
- 14.1 What Is Included?
- 14.2 Why Address GHGs in Final Design and Construction?
- 14.3 Level of Effort
- 14.4 Complementarity/Consistency with Other Transportation Goals
- 14.5 Who—Roles and Responsibilities
- 14.6 Inventory Development
- 14.7 Goal and Target Setting
- 14.8 Strategy Identification
- 14.9 Strategy Evaluation
- 14.10 Implementation
- 14.11 Monitoring, Evaluation, and Reporting
- 14.12 Self-Assessment: Final Design and Construction
14.1 What Is Included?
This stage of greenhouse gas (GHG) assessment follows the project development, preliminary design, and environmental review stages and continues towards unique or standardized specifications and special provisions for the bidding stage and for construction inspection.
Examples of GHG considerations in final design and construction include
- Selection of high-recycled-content or less-carbon-intensive materials and processes for the chosen alternative.
- Reuse of deconstructed materials.
- Equipment and fuel standards for construction equipment.
- Construction staging and detour routes.
- Buying of offsets to mitigate remaining emissions.
Figure 14.1 shows emissions sources associated with construction and maintenance of the State’s highway system for a sample composite State representing data from multiple States. Nearly 40 percent is from construction fuel, and another 40 percent is from paving materials. Overall, these emissions make up about 6 percent of total transportation-related emissions, including emissions from users of the transportation system. While this is a relatively small contribution, the department of transportation (DOT) can have direct influence over these emissions.
Figure 14.1 Emissions from Construction and Maintenance of the Transportation System
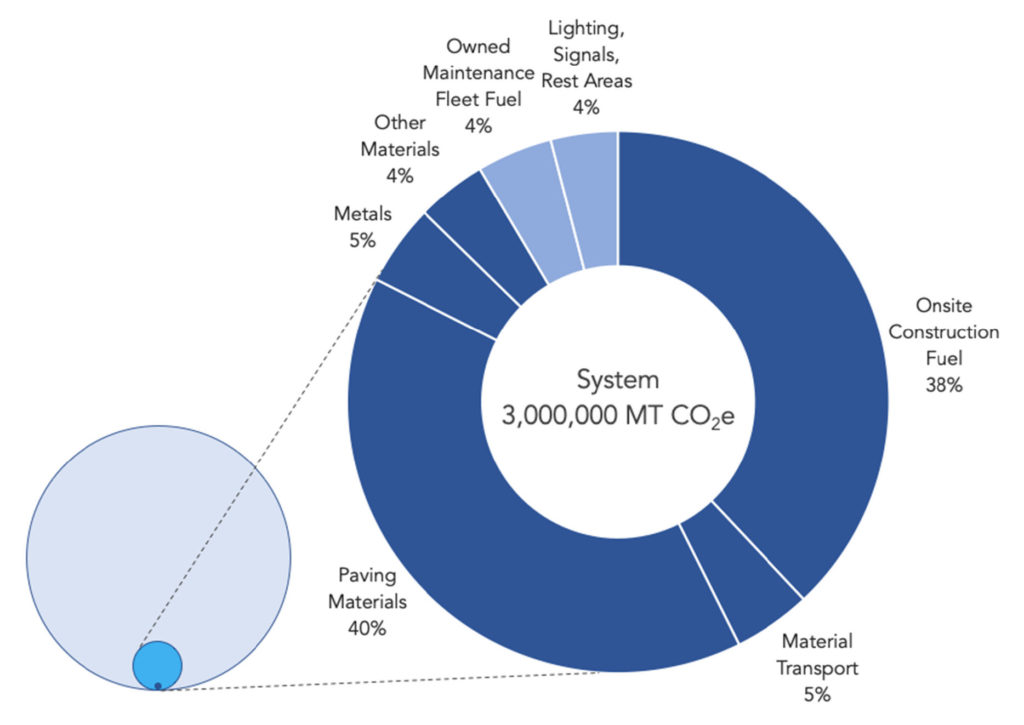
Source: Calculations by Good Company based on data from Florida, Maine, Maryland, Minnesota, Oregon, Texas, Vermont, and Washington State DOT budget documents and U.S. Environmental Protection Agency’s (EPA’s) U.S. Environmentally-Extended Input-Output (USEEIO) Model . Emissions that are primarily from construction are shown in darker blue; however, for some categories, construction and maintenance emissions cannot be clearly separated.
14.2 Why Address GHGs in Final Design and Construction?
For many public infrastructure agencies (as might be the case for a DOT if transportation system user emissions were excluded), construction is the largest source of emissions under direct control. Public infrastructure agencies have a large supply chain footprint. The chart in Figure 14.2 shows more than 40 percent of a public agency’s operational emissions coming from the supply chain; Figure 14.3 shows that nearly 40 percent of public agency supply chain emissions come from construction and maintenance activities.
Figure 14.2 Example: Public Agency Operational GHG Emissions by Source
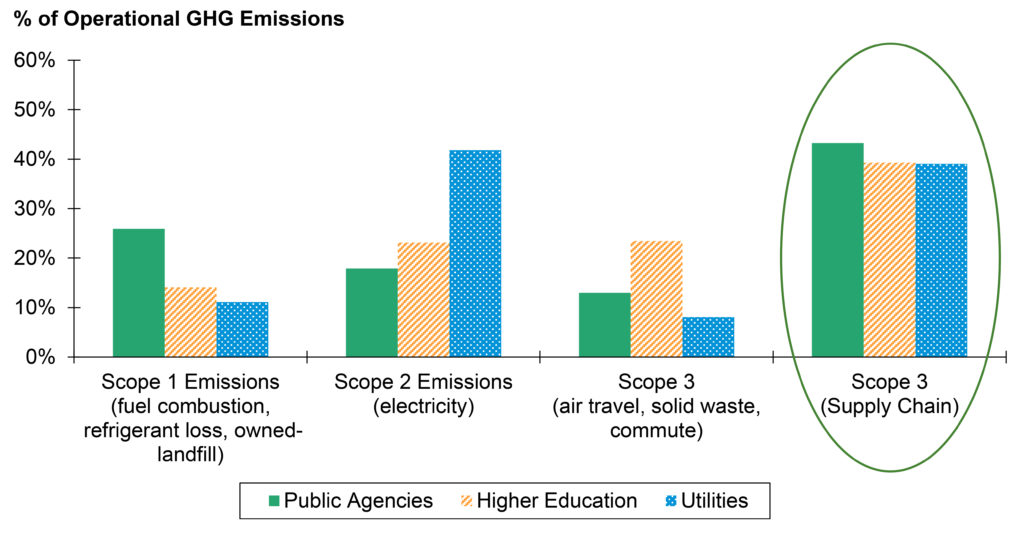
Figure 14.3 Example: Public Agency Supply Chain GHG Emissions by Source
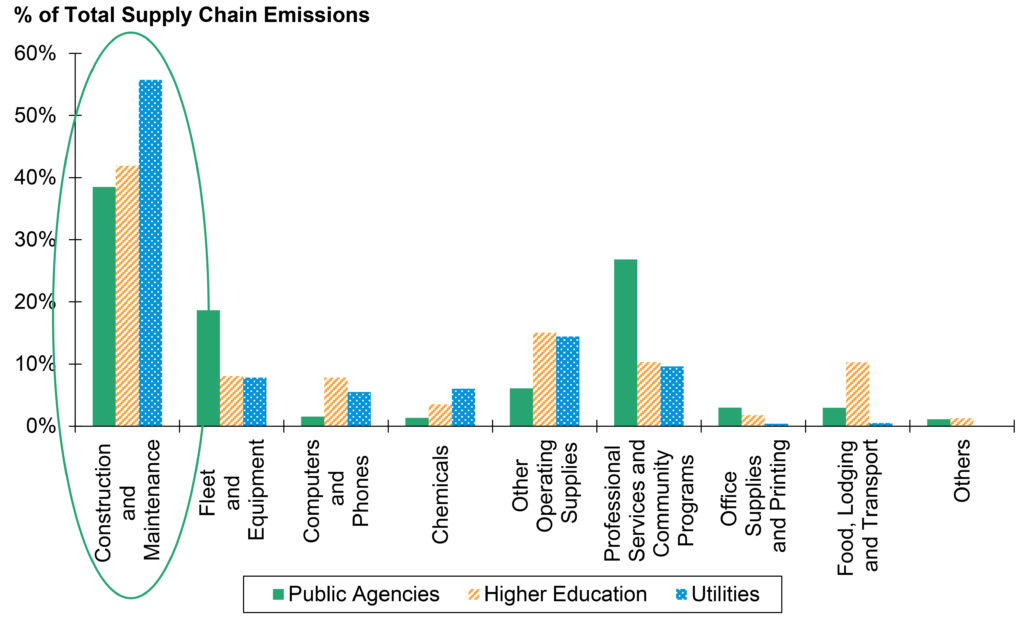
14.3 Level of Effort
14.3.1 Single Project
Consideration of GHGs in final design typically takes about 20–200 hours, with supplier research and specifications identified or developed for the project that include methods, materials, fuels, and equipment. For construction, the effort is likely 100 hours or less to ensure that the contractors are following the specifications via records checking.
Much of the analysis for any given project can be done for components of the construction process through the development of locally appropriate specifications that reduce environmental and climate impacts and reflect material supply availability. Often the materials are industrial waste products and may be less costly than standard materials. Developing the specifications for these material changes during design can help construction companies to reduce uncertainties in their bids.
14.3.2 Programmatic Approach
To avoid higher project costs and redundant research and design, standardizing specifications is the best long-term approach. Development of standard specifications will be a multiyear effort and should involve the major material suppliers. Not only do the standard specifications need to perform in the field, they also need to have a supply chain that supports them. Early projects or one-of-a-kind specifications invite higher costs, but a unified, cooperative, staged bulk buy/change of standard specifications should lower costs and eliminate the constant “reinvention of the wheel.” Furthermore, design exceptions that are done one at a time will disrupt the project schedule and possibly budget. Deviations from standard materials will almost always involve higher costs.
Environmental product declarations (EPDs) should be collected and reviewed to assess materials impacts. However, EPDs may not exist for products that have not yet been requested. For that reason, it may be most fruitful to look at the most commonly specified major material mixes, determine a lower GHG mix that serves the conditions, and then work with material producers to not only make it but also produce an EPD for it. In most States, the lower-carbon materials are made with ingredients that are less expensive than the typical Ordinary Portland Cement, but industry requires time to develop supplies that match the demand, and before this happens there is likely to be a price premium. Major materials should be redesigned carefully, with early signals to the producers so that the industry can evolve to meet the DOT’s new goals.
14.4 Complementarity/Consistency with Other Transportation Goals
GHG reduction strategies considered in the final design and construction stages can also support other goals, including
- Reductions in criteria pollutants and air toxics from construction materials transport, staging, site development, and traffic control.
- Reduction of fuel and energy consumption onsite and in production of materials.
- Reduction in environmental impacts at the materials production sites, including impacts on air quality.
- Reduction of the need for mining.
- Large-scale recycling and the use of nonvirgin materials that are often by-products generated in older processes for coal and steel production but can be used as cement substitutes. These by-products are often stored in monofils that threaten ground and surface water when not entombed in concrete.
- Economic and job development for local and regional producers of materials.
- Local agency adoption of standardized specifications that extend the benefit of the DOT work to other public infrastructure agencies.
14.5 Who—Roles and Responsibilities

Potential roles in GHG consideration in this functional area include
- Executives—Send a clear signal to the central engineering team that GHGs are to be considered, and this consideration should shape projects as one of many considerations. The degree of weight ascribed to GHG reduction compared to other considerations will likely be a function of the State’s and the DOT’s priorities. Ensure that a life-cycle approach to costs and benefits is considered. Ensure the development of standard specifications that meet local performance needs and market conditions.
- Engineering Project Manager/Materials Engineering Lead—Ensure that the analysis is done with access to information on the quantities and characteristics of the materials involved. Ensure that the information is considered and that material providers are included. Use the results to shape standard specifications as practicable.
- Specification Writer—Look first for precedent and well-established specifications that will pass all quality controls before the development of new specifications that require design exception. Many of the specifications for what may seem like a novelty in one State are common practice in another.
- DOT Project Manager/Owners Representative and Inspectors—Ensure that the specifications are properly included in the bid documents and that the contractors deliver what has been asked for at reasonable cost.
14.6 Inventory Development
This section provides an overview of emissions sources and measurement methods; specific tools and data sources are identified in Section 14.9. Most of the heavy data lift is done in the final design phase. The main activity in the construction phase is ensuring the specifications are followed or that approved equivalents are delivered for paving that has EPDs. When receipts for material quantities come in for invoicing or project closeout or as as-built designs come in, the quantities of materials, fuels, equipment, and recycled demolition/deconstruction material can be precisely determined. If a unique quantitative analysis has been done in the design phase, then the GHG inventory can be adjusted to reflect actual emissions for determining needed additional mitigations or for lessons learned.
14.6.1 Materials
For preliminary design alternatives analysis, a carbon (or GHG) footprint of the major materials should be developed with assumed traditional specifications for each material type. If the designs all use the same material, it is unnecessary to footprint the materials at this time. If the material specifications vary among alternatives, then footprinting the material types is important. Alternately, the footprinting of materials could wait until the design alternative is selected. Then the material and several other specifications could be footprinted to find the best material that fits the chosen alternative.
Baselines can be established for frequently recurring use of material types such as regionally formulated concrete and asphalt mixes. These material mixes can be calculated for a standard emissions factor to multiply by tonnage or cubic yards for quicker comparisons in the future.
For alternative materials mixes, the specifications must first be found—likely from the State standardized specifications manual or from the American Association of State Highway and Transportation Officials (AASHTO) or another credible body. The carbon footprint of these materials mixes can then be calculated by using existing factors for the individual components to develop a new emissions factor that can be quickly multiplied by quantities in the future. While all of these calculations can be done uniquely for each project, a “one at a time” approach will add time and cost burden to design and likely will bring a “one-off” price from local material providers. Therefore, the availability of these mixes should be checked as well as the scale at which they may be available at the current market price or at a lower price. Generally speaking, the higher the recycled content of the materials, the lower the cost. This is dependent on regular volumes being ordered and the supplies being ordered frequently.
14.6.2 Equipment and Fuels
The amount of fuel anticipated to be used in construction activity may be estimated from experience with projects of a similar scale. Expected hours of use should be multiplied by fuel consumption rates (gallons per hour) to obtain expected fuel consumption. Fuel consumption can then be multiplied by appropriate emission factors. Tools are available to help with calculations and default values (see below).
The U.S. EPA regularly updates Emission Factors for Greenhouse Gas Inventories, a document that provides emission factors for fuels for multiple pollutants. The U.S. Energy Information Administration also publishes CO2 emission factors for fuels, in a web page and spreadsheet titled Carbon Dioxide Emissions Coefficients by Fuel. If life-cycle emissions are being inventoried rather than just direct emissions, life-cycle emissions factors can be estimated using the Greenhouse Gases, Regulated Emissions, and Energy Use in Transportation (GREET) model from Argonne National Laboratory or carbon intensity values provided by the California Air Resources Board (CARB, 2020).
14.7 Goal and Target Setting
Goals or targets can be set for reducing emissions in construction activities, on a percentage basis, compared to standard practice. Targets are most effectively set and applied on a programmatic basis. However, they may also be set for individual major projects that have unique considerations or unique opportunities for emissions reduction.
14.8 Strategy Identification
Table 14.1 gives an overview of GHG mitigation strategies in final design and construction. Tables 14.2 and 14.3 provide more detail on and examples of specific GHG reduction strategies that can be applied in the final design and construction phase.
Table 14.1 General GHG Mitigation Methods in Final Design and Construction
Emissions Source | Potential Mitigation Methods |
Equipment | Alternative fuels Energy-efficient equipment Operating procedures (e.g., idle reduction, minimize deadheading) |
Materials | Use low-carbon virgin materials Use materials with recycled content Recycle or repurpose materials Reduce quantities used Source local materials |
Traffic | Minimize detour lengths Minimize duration of delays and volume of traffic affected Staging area location |
Table 14.2 GHG Reduction Strategies in Final Design
Strategy | Examples |
Ensure that the specifications in the bid reflect the alternatives analysis best outcome to encourage responsive bidding. | Recheck market availability and costs of the recycled content inputs—such as fly ash, pozzolan, and slag—before going to bid. |
Encourage reuse of deconstructed materials. Determine the elements of the transportation facility that can be used onsite in the job or upcycled to a purpose that displaces emissions from making these components from virgin material elsewhere. | “Tired” bridge beams that can carry a large deadload but cannot endure the average daily traffic (ADT) and the loading and offloading of an Interstate may be considered for reuse in another application, e.g., erosion control, rural bridge or alternative mode crossings where premature failure is not of significant concern. These beams often require very little treatment compared to a new structure—sometimes as little as bridge ends and new railing with a wearing surface (or not). If this is not considered, any steel beam will be assumed sold for scrap value. |
Encourage the use of locally sourced materials to minimize transport distances. | Anything heavy or voluminous. |
After the material type is selected, explore variants in mixes or material composition and availability. | Concrete made with fly ash, pozzolan, or slag is likely to have a longer cure time but may be more durable and show less wear over time. |
Specify low-carbon fuels and newer engines in special provisions to manage the equipment without idling and/or replace with electric equipment as possible. | As practicable, use electric hoists instead of small cranes operating on liquid fuels. Use low-carbon biodiesel or renewable diesel in the equipment. Seek Tier 3 and 4 engines. |
Follow detour route specifications and construction staging to minimize traffic delays and vehicle miles traveled (VMT). | Scheduling of lane closures or traffic diversions in off-peak periods. |
Table 14.3 GHG Reduction Strategies in Construction
Strategy | Examples |
Try to ensure contractors have a ready supply of recyclable materials. | Have a conversation with materials providers to encourage them to show innovation to get credit and be noticed for similar projects. |
Ensure that any reuse agreements are followed if the facility elements can be deconstructed without damage. If the damage is unavoidable, encourage recycling of the material—especially onsite, if possible. | “Tired” bridge beams that are damaged in deconstruction can be rubblized, the rebar recycled, and the rubble used as clean fill or base course onsite. |
Allow longer cure times for concrete. | Contractors tend to be inventive, e.g., formwork can be done on Fridays to avoid paying for 2 days in forms when the cure time is twice as long. Pours can be scheduled with cure time considered to avoid longer duration detours. |
Include the carbon intensity number or the feedstock source when specifying biodiesel or renewable diesel. | When possible, source from waste-based feedstocks such as waste grease or cooking oil. Soy diesel is the next best choice. Avoid palm oil diesel. |
Carefully specify detour routes and construction staging to minimize traffic delays and VMT. | Schedule lane closures or traffic diversions in off-peak periods. |
Figure 14.4 shows mitigation potential from construction and maintenance-related activities for a sample State (Oregon). Just over one-third of emissions can be mitigated through the use of renewable fuels and materials (cement and asphalt) substitutions. Note that traffic-related emissions are not included. The actual mitigation potential for any given State will depend upon the standard materials used, supply chain characteristics, types and characteristics of projects constructed, and other local conditions. Generally speaking, reducing emissions at the source is much easier than offsetting emissions with other strategies such as planting trees or adding small-scale wind or solar to projects.
Figure 14.4 Example of Mitigation Potential for Highway System Construction and Maintenance
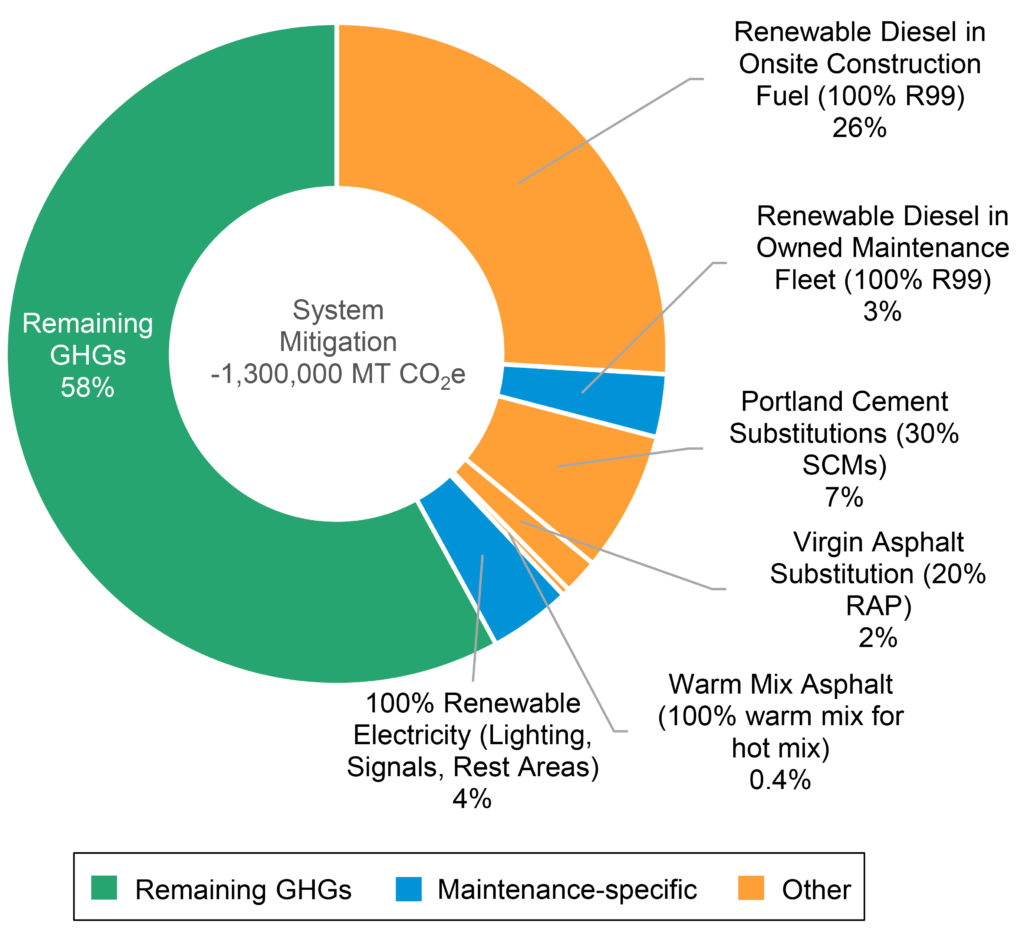
14.8.1 Low-Carbon Materials
The largest portion of construction emissions is the embodied energy and embodied emissions in major materials such as asphalt, concrete, and steel. Material choices will make a large difference in total construction and maintenance emissions. These roughly follow life-cycle costs. Higher costs up front may generate lower operating and maintenance costs later through durability.
While all three major DOT materials (asphalt, concrete, and steel) have large GHG emissions associated with their production, each material type has variations on its means of production that can reduce emissions significantly. Many of those mixes and methods have norms and standards and specifications that work and have been implemented on a wide scale. For example, high-performance concrete is used commonly for bridge decks and in saltwater environments has a longer cure time, but it includes higher percentages of fly ash content relative to traditional cement to ensure strength and wear resistance over time. Local conditions and pricing vary, but some of these GHG reduction strategies are less expensive up front and/or over the life-cycle of the facility and outperform conventional mixes.
Once the facility alternative is selected and the material types are determined, GHGs can be mitigated by looking at alternative materials that function for the same purpose and conditions, have vetted specifications, and are available in the marketplace.
14.8.2 Reuse of Deconstructed Materials
Generally speaking, if deconstructed facility components can be used as-is, this use displaces the greatest amount of emissions through the avoidance of production somewhere else, which potentially reduces the distance needed to transport materials. For example, a reused bridge beam should be deducted from the total project footprint after placement into use. Concrete pavement is treated differently. If the concrete is rubblized and used onsite as fill, subgrade, or base material, the emissions savings come from the avoidance of hauling and mining emissions (deduction), but they do not displace the production emissions of the GHG-intensive cement manufacturing. Similarly, with asphalt mixes, the use of recycled aggregate saves the mining and transport emissions, but it only slightly reduces the primary emissions source—the energy used to produce it and the asphaltic binder. For steel, generally speaking, more than 90 percent of the material in commerce is recycled content and also will be recycled in the future due to its high value.
14.8.3 Equipment and Fuel Standards
Fossil fuel consumption may be reduced by switching to biodiesel and renewable diesels, and measures such as idle reduction will reduce fuel consumption of all types. While tailpipe emissions from trucks and heavy equipment are the most obvious source of GHG emissions in construction, generally they are a small portion of the total emissions compared to the embodied emissions in the materials. Nevertheless, reducing fuel use onsite benefits air quality. Therefore, energy efficiency/GHG measures such as controlled idling should also have air quality benefits, as will more recent engines (Tier 3 and Tier 4) or electrification where possible.
For the most common uses of diesel equipment, substituting renewable or biodiesel fuel from low-carbon feedstocks will reduce GHGs more than any other fuel strategy. Renewable diesel is considered a drop-in replacement for conventional diesel but can be difficult to source. When specifying renewable diesel, check for availability and for the carbon intensity factor, which is driven by the raw feedstocks used to make it. For example, a palm-oil-based renewable diesel may have twice the GHG emissions of traditional diesel due to loss of tropical forests; whereas if renewable diesel is made with used cooking oil or another crop, it is likely to have much lower carbon intensity than traditional diesel, according to the GREET 2019 model.
14.8.4 Detour Route Analysis and Construction Staging
One clear place for reduction of GHGs is selecting the alternate routes for a detour. This analysis will not yield surprises in relative scale, as the emissions will index with the distance of the detour. To calculate the GHG emissions for the detours, multiply ADT on the affected route by the distance of the alternative route by the average U.S. fleet emissions per mile by the number of days for the detour (see sample calculations in Section 12.8). For detours that require queuing and waiting for passage, such as in the case of restricted lane access, calculate the emissions by multiplying ADT by idling emission factors by length of the wait time by the number of days for the queuing. In some cases, short-term total facility closures may be compared against longer-duration lane closures based on emissions, costs, mobility disruption, and other criteria.
The primary considerations of construction staging lend themselves to reducing GHGs. Have the staging area as close to the construction site as possible to reduce fuel use while not creating a detour situation that produces substantially more emissions from the public’s vehicles traveling greater distances. Especially with increased cure times for high-recycled-content concrete, casting the components offsite and bringing them to the site for rapid installation may result in a net increase or decrease in emissions when compared to delays or detours related to cast-in-place elements.
14.9 Strategy Evaluation
Table 14.4 includes evaluation tools and data sources for evaluating GHG emissions and reduction strategies for construction materials and fuels. Additional information on these tools is provided in Appendix B.
Table 14.4 Evaluation Tools and Data Sources for Construction, Materials, and Fuels GHG Reduction Strategies
Data Source/Tool | Material Factor | Fuel Factors | Calculation Platform | Uses for Construction Emissions Calculations |
Federal Highway Administration (FHWA) Infrastructure Carbon Estimator (ICE) | • | • | • | Planning-level tool to estimate emissions from construction materials and activity. |
FHWA LCAPave | • | Life-cycle GHG assessment for pavement. | ||
GreenDOT | • | • | • | Assessment tool and cost estimator. |
Pavement Life-Cycle Assessment Tool (PaLATE) | • | • | Life-cycle cost and environmental impacts calculator, including energy and carbon dioxide (CO2). | |
USEEIO Model | • | • | • | Emission factors of goods and services based on dollar unit costs; covers land, water, energy and mineral usage and emissions of GHGs, criteria air pollutants, nutrients, and toxics for 389 industry sectors. |
U.S. EPA Waste Reduction Model (WARM) | • | • | EPA created the WARM to help solid waste planners and organizations track and voluntarily report GHG emissions reductions, energy savings, and economic impacts from waste management practices. | |
Inventory of Carbon and Energy (ICE) | • | • | Database of embodied energy and carbon of building materials. Database provides details of original references so users can check original sources. | |
National Precast Concrete Association EPDs | • | The EPDs allow architects, engineers, building owners, and other specifiers to better understand the environmental impacts of precast and prestressed concrete products. | ||
FHWA EPDs | • | Full life-cycle environmental data for common DOT purchased materials and products. | ||
National Asphalt Pavement Association’s EPDs | • | Full life-cycle environmental data for asphalt. | ||
Portland Cement Association Environmental Impact Reporting | • | Full life-cycle environmental data for cement products. | ||
Individual producers’ EPDs | • | Must request. Not commonly done by providers. | ||
Alternative Fuel Life-Cycle Environmental and Economic Transportation (AFLEET) | • | • | Spreadsheet-based tool that calculates and compares the costs and environmental benefits of a broad range of alternative fuels and vehicle technologies. | |
Heavy-Duty Vehicle Emissions Calculator (HDVEC) | • | • | Tool to aid fleets and decision-makers to compare vehicle technologies for emission reductions and consider allocation of funding. | |
U.S. EPA DEQ | • | • | Evaluates clean diesel projects and upgrade options for medium-heavy-duty and heavy-heavy-duty diesel engines. Estimates baseline emissions, reduced emissions, cost effectiveness for NOx, particulate matter (PM)2.5, hydrocarbons (HCs), carbon monoxide (CO) and CO2, and PM-related health benefits. | |
Carbon Intensity Factors—CARB (2020) | • | Life-cycle GHG emission intensity factors for fuels. | ||
North Carolina State’s Tree and Grass Carbon Calculator | • | • | Calculate sequestration of carbon from vegetation for mitigation purposes. | |
United States Forest Service 1605b Forestry Tables | • | Methods for calculating forest ecosystem and harvested carbon, with standard estimates for forest types of the United States. |
Example: Life-Cycle GHG Emissions from a Bridge Replacement in Portland, Oregon
The Portland Bureau of Transportation (PBOT) had to replace a bridge with a wood substructure after a fire that damaged the facility. PBOT requested GHG analysis for the three proposed alternatives, selection of materials types, and mitigation strategies to offset emissions. Three sources of emissions were studied—embodied emissions, emissions from transport of materials, and disposal emissions. A variety of mitigation strategies was considered. Emissions related to traffic using the bridge were not included in the analysis, but a rough estimate of these emissions was made by the project team to place the various emissions sources in context.
Key findings include the following:
- For this bridge, the largest emissions benefit was from reuse of deconstructed materials in other applications (“materials management”) (see Figure 14.5).
- Use of recycled content in material mixes could reduce the life-cycle emissions of the bridge facility by approximately 30 percent above and beyond the 10–15 percent reduction from fly ash content of the concrete mixes originally specified.
- Switching fuel to lower-carbon diesel is an easy change with results—but use of fuel onsite and for delivery of materials is a smaller portion of emissions than may be expected.
- The cost of purchasing carbon offsets instead of implementing any technical strategies is equal to about $44,000 for the life-cycle GHG emissions. The cost of offsets may be smaller than making any technical changes that reduce the equivalent GHGs in the unique project.
- Reducing trip lengths for vehicles currently detoured around the bridge will reduce CO2 equivalents by about 25,000 mt over the bridge’s 75-year lifespan or about 10 times the maximum reduction of 2,600 mt from mitigation strategies.
Figure 14.5 GHG Mitigation Potential from Example Bridge Replacement Project
Source: Good Company, 2010.
For more detail on this example, see Appendix C.14.10 Implementation
In this stage, implementation is really ensuring the specifications are properly developed and vetted in the marketplace before being put out to bid. It also is a matter of inspection and enforcement of the specifications. Implementation follows the standard “Plan, Do, Check, Act (Improve)” cycle typically employed by DOT organizations (Table 14.5).
Table 14.5 GHG Management Cycle: Final Design and Construction
Plan | Set policy | Establish targets | Make assignments |
Do | Develop procedures | Train staff | Implement |
Check | Report | Consolidate reports | Evaluate performance |
Act (Improve) | Check in agencywide | Explore alternatives | Revise procedures |
Source: Adapted from Using an Environmental Management System to Meet Transportation Challenges and Opportunities: An Implementation Guide (AASHTO, 2003) and Beyond the Short-Term—Transportation Asset Management for Long-Term Sustainability, Accountability and Performance (FHWA, 2010b).
14.11 Monitoring, Evaluation, and Reporting
Monitoring of performance for final design and construction in the “Plan, Do, Check, Act” context is mainly an oversight function of assessing how well the specifications for the preferred methods and materials are performing in the field, evaluating this performance, reporting progress on an agency basis, and making improvements in process and specifications for the next cycle. While it is possible to compare projected emission reductions with actual ones on a project-by-project basis, if procedures are enforced, emission results should not vary markedly from project estimates, and programmatic totals may be used in calculating results.
In reporting to the public, the original alternatives analysis should be described as well as how GHG considerations have shaped the project and reduced its carbon footprint. Total GHG reductions from all projects considering new GHG-compliant specifications and practices should also be reported.
14.12 Self-Assessment: Final Design and Construction
A self-assessment worksheet is provided to assist State DOT staff involved in final design and construction to determine their level of engagement in GHG assessment and additional steps they could take to estimate and reduce GHG emissions. The worksheet is meant to be used as a guide and completed with any markings and notes that are helpful.
Click to download – Self-Assessment: 14.0 Final Design and Construction