Culture Development/Management – Safety and Collaboration
While not technically a phase within the construction safety and phasing plan (CSPP) process, developing and continuing to promote a spirit of safety and collaboration throughout all portions of the CSPP process was found to be critical to the successful development, implementation, and management of a CSPP. As a result, it is a foundational element of the entire CSPP process as shown in the graphic below.
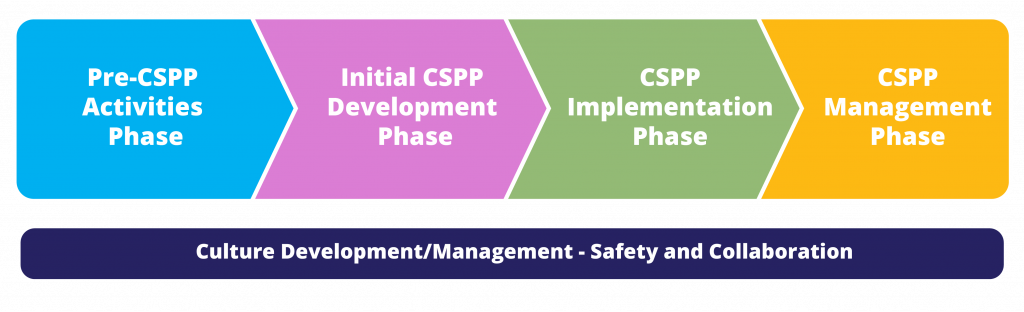
Details regarding the specific focus and activities related to developing and managing a culture of safety and collaboration are included on the webpage for each of the four CSPP phases.
Best Practices/Lessons Learned
As part of ACRP Project 08-03, a number of best practices/lessons learned (BP/LL) were identified for the Culture Development/Management – Safety and Collaboration foundation that supports the entire CSPP process. Please note that some BP/LL may appear in multiple phases of the CSPP process as some BP/LL are applicable to multiple phases.
The BP/LL identified for the Culture Development/Management – Safety and Collaboration foundation are listed below:
Best Practices for Continuously Reinforcing Safety: Safety should be promoted and discussed throughout a project. Below are some best practices for reinforcing safety throughout the duration of a construction project:
- Complete a safety briefing with contractor staff before every shift,
- Complete rotating “tool box” talks on different safety items,
- Start all construction project meetings with a discussion on safety and any safety issues that need to be addressed,
- Utilize current news stories to reinforce safety messages and the importance of safety, and
- Develop an airside safety tool kit for contractors.
These best practices support the continued reinforcement of the importance of safety. If the contractor has personnel who are not fluent in English, consideration should be given to developing safety promotion materials in other languages and ensuring interpreters (e.g., bilingual contractor personnel) are available during meetings to communicate messages in other languages.
Cultivate a Team Environment with a Focus on Safety: While this isn’t specifically related to the development of CSPPs and safety plan compliance documents (SPCDs), the importance of having a strong safety culture and cultivating a team environment was identified as a best practice for ensuring good planning related to the development of CSPPs and SPCDs. This is especially important for airport personnel, the project consulting engineer/designer, and the contractor.
Develop an Airport-Specific Airside Safety Tool Kit for Contractors: Airports with regular construction activity should consider the development of an airside safety tool kit that can be used to reinforce construction safety practices with contractors. The tool kit should include electronic and printable publications that the contractor can provide to construction personnel. Graphics or videos should be used as frequently as possible within the tool kit publications to support the communication of safety messages across language barriers. Bilingual tool kit materials should be developed, where appropriate. The tool kit should be closely tied to the airport’s contractor training program.
Develop an Airport-Specific Contractor Training Program: Airports with regular construction activity should consider the development of a formal airside construction safety training program for contractors that can instill and reinforce construction safety practices related to the airfield. This training should be in addition to the training required under federal regulations (e.g., security training, airfield driver’s training) and should focus specifically on the construction safety and phasing requirements of the project. Topics that could be part of this training include but are not limited to
- Aircraft operational patterns in the work area;
- Protected surfaces [runway safety area (RSA), object free area (OFA), Part 77, navigational aids (NAVAIDs) critical areas, etc.] surrounding the work area;
- Haul route familiarization;
- Closure request processes; and
- Foreign object debris (FOD) control.
If the airport has a contractor permitting process, these training requirements should be integrated with the permitting process to ensure the contractor does not receive a work permit until all required training is completed. It is important that the training program include recurrent training during long-duration projects and ongoing training (as needed) when new construction personnel are hired or when various subcontractors begin working. Diversity within the contractor workforce should be considered in the development and delivery of the training program. Videos and graphics should be utilized as much as possible to communicate safety messages across language barriers. If the airport commonly has contractor personnel that do not fluently speak English, the development of training materials in other languages should be considered. At airports where creating a contractor training program may not be practical, airport staff should at least talk with contractor staff to provide a brief orientation regarding working on the airfield and specific safety expectations. The contractor training guide developed as a deliverable of this project can be used as a starting point for developing an airport-specific program.
“CliffsNotes” CSPP Version: Some personnel may not be able to carry a full version of the CSPP with them at all times while they are working at the construction site. In these cases, a “CliffsNotes” or summary version of the key items in the CSPP should be provided for them (electronic or hard copy) to be able to reference.
Phase “Flash Cards”: Every day during the initial safety briefing before construction activities begin, the contractor should consider providing employees with a “flash card” notating the phase being worked on that day, areas they are to stay clear of, haul routes to be used, etc. This can help ensure that contractor staff do not get confused on the differences between each phase of the project. This is especially important for complex projects with multiple phases. These “flash cards” can also be made into smaller wallet-sized cards that could be connected to a lanyard or stored wherever an individual’s airport identification badge is displayed. Contact information for key members of the project team can also be included on the card.
Contractor “Buddy” System: Anytime a new contractor employee begins working on the airfield, they should be assigned to another contractor employee (or a “buddy”) who is more experienced with airfield construction. This provides the new employee with a person who can help educate them about items to be aware of during construction activities on an airfield and observe their compliance with safety practices. Some contractors give new personnel a different color of hard hat (or place stickers on their hard hats) so that more experienced personnel can easily identify new personnel.
Planning for Phase Changes During Construction: While a construction project is underway, the contractor should develop communication/education strategies to ensure their staff are aware of any changes associated with the start of a new construction phase (e.g., changing haul routes, protected areas). This communication should be carefully coordinated with the airport sponsor and consulting engineer/designer.